|
|
|
Submersible Sludge Pump |
|
Product Introduction: |
Overview |
|
NSQ submersible sludge pump is hydraulic machinery, the motor and the pump of which are coaxially submerged in medium to work. The overflowing parts of the pump are made from high alloy wear-resistant material, so the pump has good wear resistance and large flowing passage. It is applicable for conveying media such as sludge, ore slurry, coal slurry, sandstones containing big solid particles. The product is designed and manufactured by domestic and oversea advanced technologies. Besides the main impeller, the bottom of the pump is additionally provided with a set of agitation impeller which can spray the deposited sludge into turbulent flow, and therefore the pump realizes high-concentration conveying under the condition of no auxiliary device. The unique seal device can effectively balance the pressure inside and outside the oil chamber, so as to protect the reliability of the mechanical seal to the maximum extent. The motor adopts various protective measures such as overheat protection, water inlet detecting protection, and can operate safely for a long term in harsh working conditions.
The pump is applicable for pumping sand for building, silty sand, silt, tailing slurry, ore, iron sand ore, sediment in sewage treatment works, etc. |
|
Model Implication |
|
|
|
Structural Property |
|
1.The whole machine is dry submersible pump, and the motor adopts oil chamber seal mode and is provided with mechanical seal inside, so that high pressure water and impurities are effectively prevented from entering inner cavity of the motor.
2.Besides the main impeller, there is the agitation impeller which can agitate the sludge deposited on the water bottom into turbulent flow and pump the sludge out.
3.The trans-flux parts such as the impeller and the agitation impeller are made from high-hardness high chromium cast steel, have wear resistance, corrosion resistance and strong drainage capacity, and allow big solid particles to pass.
4.The motor is submerged in water, is not limited by suction stroke, and has high sludge suction rate and thorough desilting.
5.The integral device is simplified, needs no auxiliary stirrer device or ejector device, and has simple and convenient operation and low total investment of the unit.
6.The agitation impeller directly approaches the depositional surface, and controls the concentration through submerged depth. Under the condition of large medium proportion, an auxiliary device can be arranged to increase the concentration of the medium.
|
|
Use Conditions |
|
1.The power source is 50Hz/380V three-phase alternating-current supply, and the capacity of the substation transformator is two to three times of the rated capacity of the motor.
2.The temperature of the medium cannot exceed 60℃, and the medium does not contain inflammable or explosive gases.
3.The maximum weight concentration of the solid particles in the medium: the maximum weight concentration of the ash is 45% and the maximum weight concentration of the slag is 60%.
4.The submerged depth of the unit is not more than 20 meters, and the minimum submerged depth takes submerging of the motor as reference.
5.The unit works in the medium vertically, and the working status is continuous. |
|
Product Selection |
|
NSQ submersible sludge pump has many specifications to meet different working conditions of different users. As long as specifications and modes meeting the working conditions are reasonably and correctly selected, the best benefit can be obtained with less investment; simultaneously, reasonable working conditions can effectively prolong the service life of the pump, and the methods are as follows:
1. Whether the field conditions (such as voltage, frequency, water quality, power source and capacity) accords with the use conditions is mastered.
2. The pump specification is selected:
1) Initial selection of the flow rate: the flow rate of the pump is determined according to demands.
2) Determination of pipes:critical sedimentation flow velocity is calculated according to the conveyed medium, so as to reasonably select the pipe diameter.
3) Calculation of pipe loss: the pipe loss is calculated according to the length of the pipe and the number of the syphons and valves.
4)Calculation of the pump lift: the pump lift=vertical height difference from the water surface to the water outlet + pipe loss + outlet pressure+safety margin (10%)
5)The pump specification is determined according to the pump lift and flow rate.
6)The installation mode is determined: fixed mode and mobile mode.
3. Friendly Tips
1)Only closed system has outlet pressure, and the outlet pressure of the open system is zero.
2)The power of the matched motor of the pump is calculated according to intermediate concentration (the medium density is 1.3.), and the power should be rechecked when the pump is used for high-concentration conveying.
3) when the medium cannot submerge the motor or the temperature of the medium is more than 60℃, a cooling shield is adopted for forced cooling, the pressure of the cooling water is 2-3kg, and the flow rate of the cooling water is 5-8 m3/h.
4)The outlet of the pump should be provided with a valve; when the pump is started, the valve should be closed and then the motor is started, and the valve is gradually opened after the motor normally rotates.
5)The valve should be closed first and then the power source is cut off when the pump is shut down, so as to prevent water hammer in the pipe from severely damaging the pump.
6)In order to prevent blockage of the pipe, clear water should be conveyed for a while to clean the pipe before machine halt, until clear water flows out from the water outlet. |
|
Performance Parameters and Curve |
|
No. |
Model |
Flow Rate m3/h |
Pump Lift m |
Motor Power kw |
Speed r/min |
Efficiency |
Discontinously Passed Maximum Particle Size mm |
Water Outlet Diameter mm |
Production Status |
1 |
NSQ30-30-7.5 |
24 |
31 |
7.5 |
1460 |
43 |
13 |
80 |
√ |
30 |
30 |
36 |
29 |
2 |
NSQ50-21-11 |
35 |
22 |
11 |
1460 |
48 |
21 |
100 |
※ |
50 |
21 |
60 |
20 |
3 |
NSQ100-16-11 |
70 |
20 |
11 |
1460 |
55 |
21 |
100 |
√ |
100 |
16 |
120 |
15 |
4 |
NSQ50-26-15 |
35 |
29 |
15 |
1460 |
48 |
13 |
80 |
√ |
50 |
26 |
60 |
24 |
5 |
NSQ60-30-15 |
42 |
33 |
15 |
1460 |
50 |
13 |
100 |
√ |
60 |
30 |
72 |
27 |
6 |
NSQ100-18-15 |
70 |
20 |
15 |
1460 |
55 |
21 |
100 |
√ |
100 |
18 |
120 |
15 |
7 |
NSQ150-15-15 |
105 |
17 |
15 |
1460 |
56 |
21 |
150 |
√ |
150 |
15 |
180 |
13 |
7 |
NSQ150-15-15 |
105 |
17 |
15 |
1460 |
56 |
21 |
150 |
√ |
150 |
15 |
180 |
13 |
8 |
NSQ150-22-22 |
105 |
25 |
22 |
980 |
60 |
32 |
150 |
√ |
150 |
22 |
180 |
20 |
9 |
NSQ200-15-22 |
140 |
17 |
22 |
980 |
60 |
45 |
150 |
√ |
200 |
15 |
240 |
13.5 |
10 |
NSQ150-30-30 |
105 |
33 |
30 |
980 |
50 |
21 |
150 |
√ |
150 |
30 |
180 |
26 |
11 |
NSQ300-20-37 |
240 |
22 |
37 |
980 |
58 |
28 |
150 |
√ |
300 |
20 |
360 |
17 |
12 |
NSQ200-30-45 |
140 |
33 |
45 |
980 |
53 |
25 |
150 |
√ |
200 |
30 |
240 |
27 |
13 |
NSQ150-45-55 |
105 |
47 |
55 |
980 |
50 |
21 |
150 |
√ |
150 |
45 |
180 |
42 |
14 |
NSQ250-35-55 |
175 |
38 |
55 |
980 |
53 |
36 |
150 |
√ |
250 |
35 |
300 |
33 |
15 |
NSQ600-15-55 |
420 |
18 |
55 |
980 |
62 |
32 |
250 |
★ |
600 |
15 |
720 |
11 |
16 |
. NSQ200-45-75 |
140 |
48 |
75 |
980 |
52 |
18 |
150 |
√ |
200 |
45 |
240 |
41 |
17 |
NSQ400-25-75 |
280 |
29 |
75 |
980 |
62 |
29 |
200 |
※ |
400 |
25 |
480 |
23 |
18 |
NSQ500-25-90 |
350 |
30 |
90 |
980 |
65 |
25 |
200 |
√ |
500 |
25 |
600 |
20 |
19 |
NSQ400-50-110 |
280 |
54 |
110 |
980 |
56 |
28 |
200 |
※ |
400 |
50 |
480 |
45 |
20 |
NSQ1000-18-110 |
700 |
22 |
110 |
980 |
68 |
50 |
300 |
√ |
1000 |
18 |
1200 |
13 |
21 |
NSQ780-26-110 |
545 |
29 |
110 |
980 |
68 |
50 |
300 |
√ |
780 |
26 |
935 |
22 |
22 |
NSQ400-60-132 |
280 |
64 |
132 |
980 |
68 |
28 |
200 |
★ |
400 |
60 |
480 |
55 |
23 |
NSQ500-45-132 |
350 |
49 |
132 |
980 |
67 |
28 |
200 |
√ |
500 |
45 |
600 |
42 |
24 |
NSQ500-55-132 |
350 |
59 |
132 |
980 |
70 |
28 |
200 |
√ |
500 |
55 |
600 |
52 |
25 |
NSQ800-35-132 |
560 |
38 |
132 |
980 |
70 |
42 |
300 |
√ |
800 |
35 |
960 |
32 |
26 |
NSQ1000-22-132 |
700 |
27 |
132 |
980 |
71 |
50 |
300 |
√ |
1000 |
22 |
1200 |
17 |
27 |
NSQ650-52-160 |
455 |
56 |
160 |
980 |
65 |
28 |
200 |
√ |
650 |
52 |
780 |
44 |
28 |
NSQ600-55-200 |
420 |
59 |
200 |
980 |
62 |
28 |
250 |
√ |
600 |
55 |
720 |
50 |
29 |
NSQ800-55-220 |
560 |
60 |
220 |
980 |
66 |
38 |
300 |
√ |
800 |
55 |
960 |
50 |
30 |
NSQ1250-35-220 |
875 |
39 |
220 |
980 |
70 |
45 |
350 |
※ |
1250 |
35 |
1500 |
30 |
31 |
NSQ1500-35-250 |
1050 |
40 |
250 |
980 |
72 |
50 |
350 |
★ |
1500 |
35 |
1800 |
30 |
32 |
NSQ1750-30-250 |
1225 |
34 |
250 |
980 |
70 |
55 |
350 |
※ |
1750 |
30 |
2100 |
25 |
33 |
NSQ2000-35-315 |
1400 |
40 |
315 |
980 |
72 |
60 |
400 |
★ |
2000 |
35 |
2400 |
30 |
Products marked with √ are conventional products, products marked with ※ are modified products, the products marked with ★ are those which have drawings but have not been developed, and the custom and supply period of the undeveloped products is 45-60 days. |
|
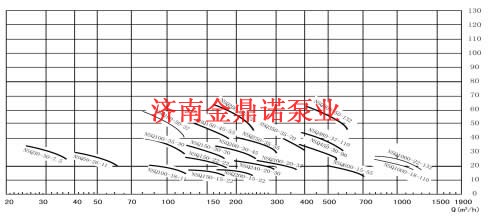
|
|
|
|
No. |
Model |
L (mm) |
L1 (mm) |
L2 (mm) |
A (mm) |
B (mm) |
C (mm) |
d (mm) |
1 |
NSQ30-30-7.5 |
842 |
700 |
296 |
605 |
390 |
396 |
80 |
2 |
NSQ50-21-11 |
913 |
738 |
300 |
606 |
406 |
405 |
100 |
3 |
NSQ100-18-11 |
913 |
738 |
300 |
606 |
406 |
405 |
100 |
4 |
NSQ50-26-15 |
950 |
774 |
300 |
640 |
385 |
422 |
80 |
5 |
NSQ60-30-15 |
950 |
774 |
290 |
632 |
385 |
422 |
100 |
6 |
NSQ100-18-15 |
950 |
774 |
300 |
640 |
385 |
422 |
100 |
7 |
NSQ150-15-15 |
990 |
814 |
340 |
620 |
410 |
455 |
150 |
8 |
NSQ150-22-22 |
1401 |
1135 |
535 |
883 |
630 |
568 |
150 |
9 |
NSQ200-15-22 |
1375 |
1110 |
507 |
870 |
630 |
551 |
150 |
10 |
NSQ150-30-30 |
1452 |
1144 |
425 |
832 |
630 |
605 |
150 |
11 |
NSQ300-20-37 |
1567 |
1170 |
510 |
1070 |
595 |
775 |
150 |
12 |
NSQ200-30-45 |
1699 |
1255 |
495 |
1006 |
665 |
650 |
150 |
13 |
NSQ150-45-55 |
1692 |
1248 |
488 |
1011 |
678 |
640 |
150 |
14 |
NSQ250-35-55 |
1699 |
1255 |
495 |
1006 |
665 |
650 |
150 |
15 |
NSQ600-15-55 |
1720 |
1275 |
515 |
1052 |
711 |
675 |
250 |
16 |
NSQ200-45-75 |
1904 |
1425 |
488 |
1011 |
678 |
640 |
150 |
17 |
NSQ400-25-75 |
1888 |
1410 |
485 |
1422 |
665 |
1047 |
200 |
18 |
NSQ500-25-90 |
1888 |
1410 |
485 |
1422 |
665 |
1047 |
200 |
19 |
NSQ400-50-110 |
2225 |
1550 |
500 |
1190 |
760 |
790 |
200 |
20 |
NSQ1000-18-110 |
2407 |
1725 |
626 |
1640 |
854 |
1207 |
300 |
21 |
NSQ780-26-110 |
2407 |
1725 |
626 |
1640 |
854 |
1207 |
300 |
22 |
NSQ400-60-132 |
2328 |
1665 |
520 |
1540 |
849
|
1117 |
200 |
23 |
NSQ500-45-132 |
2320 |
1656 |
472 |
1124 |
823 |
739 |
200 |
24 |
NSQ500-55-132 |
2320 |
1656 |
472 |
1124 |
823 |
739 |
200 |
25 |
NSQ800-35-132 |
2538 |
1784 |
601 |
1581 |
802 |
1177 |
300 |
26 |
NSQ1000-22-132 |
2465 |
1801 |
626 |
1640 |
854 |
1207 |
300 |
27 |
NSQ650-52-160 |
2673 |
1772 |
472 |
1124 |
823 |
739 |
200 |
28 |
NSQ600-55-200 |
2673 |
1772 |
472 |
1140 |
823 |
739 |
250 |
29 |
NSQ800-55-220 |
2934 |
1993 |
710 |
1686 |
900 |
1229 |
300 |
30 |
NSQ1250-35-220 |
2922 |
2021 |
730 |
2150 |
977 |
1630 |
350 |
31 |
NSQ1500-35-250 |
3012 |
2111 |
730 |
2150 |
977 |
1630 |
350 |
32 |
NSQ1750-30-250 |
3012 |
2111 |
730 |
2150 |
977 |
1630 |
350 |
33 |
NSQ2000-35-315 |
3235 |
2261 |
804 |
2260 |
1026 |
1730 |
400 | |
|
Installation and Application Instruction |
|
1、Preparation before Installation
1)Carefully check whether the electric pump is deformed or damaged in the processes of transport, storage and installation and whether the fastening pieces are loosened or fallen off before starting.
2)Check whether the cable is damaged or broken, if yes, replace the cable to avoid electric leakage.
3)Check whether the power source device is safe and reliable and that the rated voltage should accord with the nameplate.
4)Use a megohmmeter to check that the motor stator winding cold ground insulation resistance should not be less than 50MΏ.
5)Check whether the oil quantity in the oil chamber is appropriate and that the oil level of the unit in the vertical position should be flush with the oil filling opening.
6)Make sure that clear cold water is filled continuously when the submersible pump with the cooling shield is started, and make sure that the outlet is smooth and the cooling water flows in from one side of the lower end and flows out from the upper end of the other side.
2、Notices
After the pump is operated normally, please observe whether the voltage of the power source, the working current, the flow rate of the pump and the vibration of the pump are normal at any time. If one of the following conditions occurs, please immediately stop the machine to check:
1)The working current exceeds the rated current. 2)In the rated pump lift, the flow rate is reduced by more than 20% or the water outlet is discontinuous. 3)The voltage of the power source is overhigh or too low. 4)The pump has obvious vibration or noise.
3、Installation Notices
1)Electrical connection: the electrical connection should be carried out by professional electrician according to the circuit diagram, the insulation resistance should be detected at any time in the installation process, and the motor insulation resistance should not be less than 5MΏ after the installation is over. The pump is hung and subjected to inching turning, so as to observe its rotation direction, and the pump is rotated clockwise if a person looks downward from the motor direction. If the rotation direction is wrong, please replace any two connectors of the three phase power supply.
2)Prohibit using the cable of the pump as a rope for installation and hoisting, so as to avoid dangers.
3)The pump should be vertically submerged in water, should not be horizontally placed and fall into sludge, and the power source should be cut off when the pump is moved.
4、Storage Notices
1)The electric pump should be placed into clear water to rotate for several minutes after being used for many times, so as to prevent sediment from remaining in the pump and ensure the cleanness of the electric pump.
2)The electric pump should be taken out from water if not used for a long term, so as to reduce the occasion that the motor stator winding is affected with damp and prolong the service life of the electric pump.
3)Under normal working conditions, the electric pump should be maintained after working for a year, the worn wearing parts should be replaced, the tightening status should be checked, and the lubricating grease of the bearing and the insulating oil in the oil chamber should be replenished or replaced, so as to ensure good operation of the electric pump. |
|
Application Cases |
|
|
|
|
Sketch Map of Agitation Effect in Water |
Safe Agitation Range of the Electric Pump with the Agitation Impeller |
Yellow River Desilting Project |
|
|
|
Sketch Map of DPB Electric Pump Platform Parallel Desilting Equipment |
|
|
|
|
|
|
|
Causes of Faults and Countermeasures |
|
Faults |
Possible Causes |
Solution |
The current is overhigh and exceeds the rated current. |
1. The pump is friction-resistant. |
1. adjusting the clearance |
2.The pump lift of the device is too low and the pump is operated in larger flow rate. |
2. controlling the flow rate by the valve or replacing a pump with proper pump lift |
3. The bearing is damaged. |
3. replacing the bearing |
The motor does not rotate and has noise when started. |
1. The voltage is too low |
1.adjusting the voltage to the rated value |
2. The motor is rotated with single phase. |
2. checking the lines and connecting the broken lines |
3. The pump is blocked by foreign matters. |
3. removing the foreign matters |
4. The impeller rubs with the inner pump cover or the water suction plate. |
4. adjusting the clearance of the impeller to normal value |
The pump does not output water or output a small quantity of water. |
1. The impeller rotates reversely. |
1. changing any two phase power cords |
2.Water strainer is blocked. |
2. removing the blockage |
3. The water inlet is exposed out of the water surface. |
3. adjusting the pump to submerge the pump |
4. Water pipe leaks or are leaked. |
4. replacing the water pipe or removing the sludge |
5. The actual pump lift is too high. |
5. selecting a pump with proper pump lift |
The insulation resistance is reduced to below 0.5 MΏ. |
1. Cable connector is damaged. |
1. treatingthe cable connector again |
2. The stator winding insulation is damaged. |
2. replacing the stator winding |
3. Water enters the cavity of the motor. |
3. removing the water content and drying the winding |
4. The cable is damaged. |
4. repairing the cable |
The pump has unstable operation and serious vibration. |
1. The impeller is worn seriously. |
1. replacing the impeller |
2. Impurities block the rotating parts. |
2. clearing the impurities |
3. The bearing is damaged. |
3. replacing the bearing | |
|
|
|
|
|
 |
|